Frankb
Well-Known Member
400/512, Trick Flow intake, Trick Flow 240 heads. All parts installed new out of box. Low mileage engine, 300-400 miles since built, probably less. Putting smaller intake on so hood can go back on. When I removed Trick Flow intake there was oil on the intake/head mating surface. Oil is on both intake and head. About same amount of oil on passenger and driver side of intake.
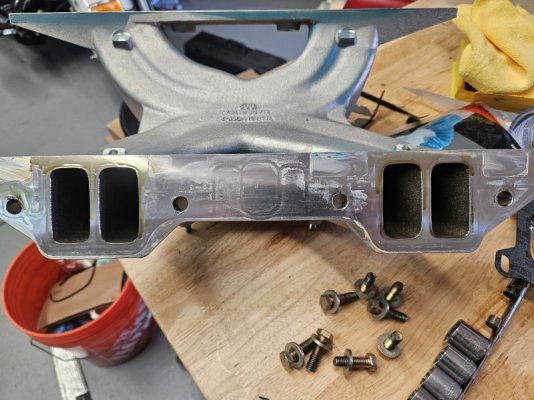
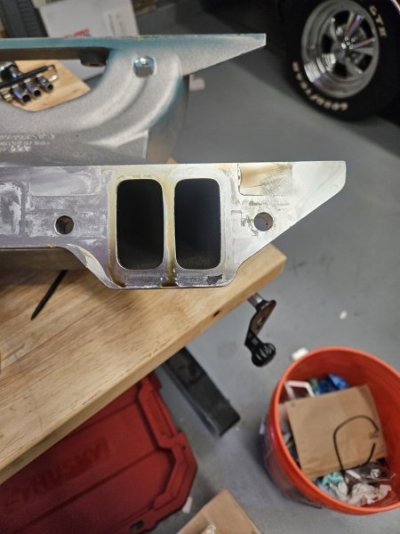
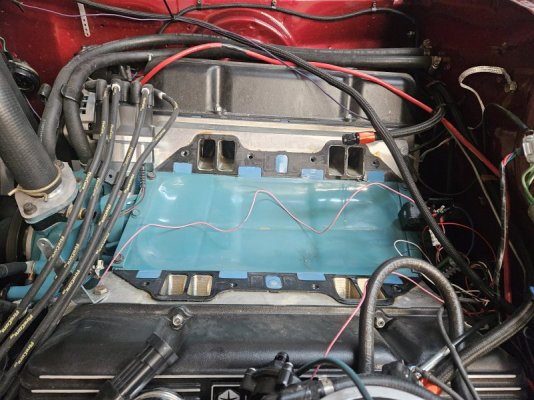
Additionally, there looks to be a fine mist of oil/gas on head intake runners. Most heavy in #5 and #7 I’ve never seen this before. Car ran excellent. No oil consumption noted. No oil smoke from exhaust noted. Carb is Sniper FI. Is there a problem here? Where did this oil come from?
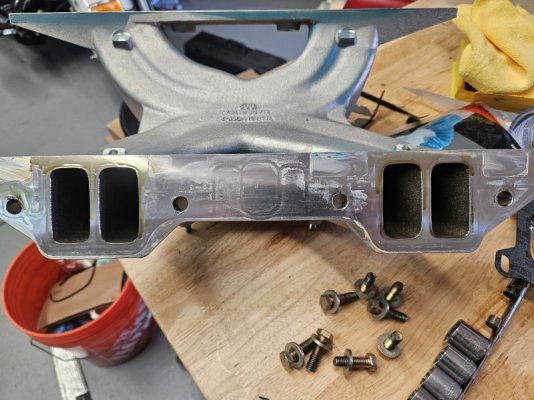
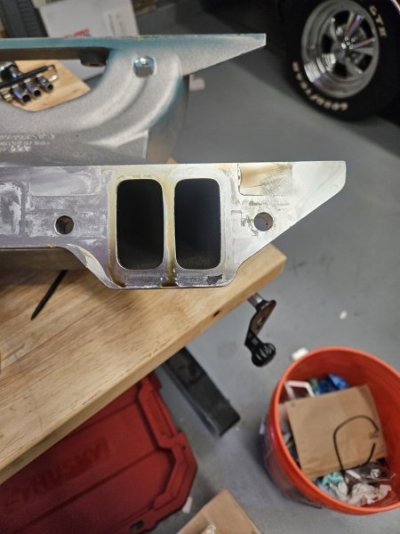
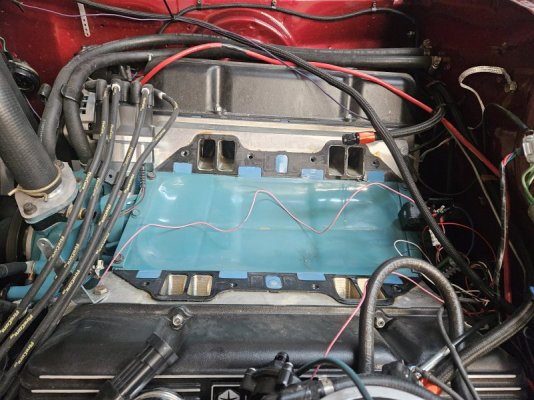
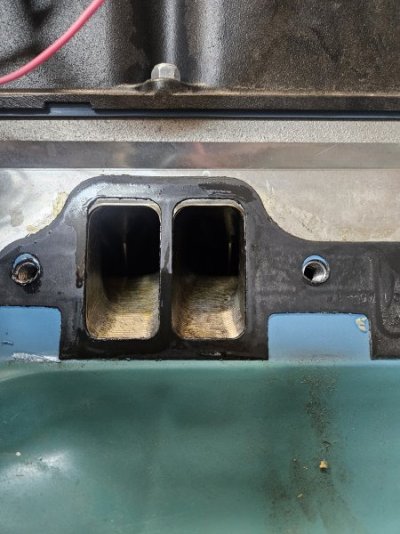