james j
Member
Hi Guys!
I'm a little new here, but I am finally getting back to my project. I'm have a '68 charger and am putting the spring relocation kit coupled with mini-tubs. While I have the new spring pockets are already installed in the frame rails, I have the new leaf spring perches just tacked in place on the rear end (which still has its axles in it). As such, I just wanted to see if you have any advice on how to finish the welds on new perches. I figure that it would be easier to ask, since I am concerned about warping. The rear end still has it's original axles in it, but they will be replaced before they go back in the car.
Any hints or advice would be greatly appreciated.
Thanks,
James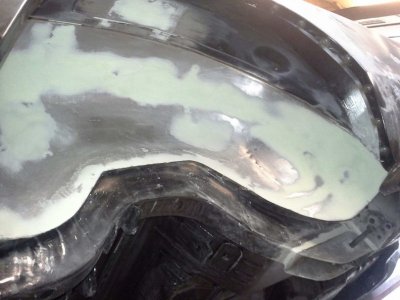
I'm a little new here, but I am finally getting back to my project. I'm have a '68 charger and am putting the spring relocation kit coupled with mini-tubs. While I have the new spring pockets are already installed in the frame rails, I have the new leaf spring perches just tacked in place on the rear end (which still has its axles in it). As such, I just wanted to see if you have any advice on how to finish the welds on new perches. I figure that it would be easier to ask, since I am concerned about warping. The rear end still has it's original axles in it, but they will be replaced before they go back in the car.
Any hints or advice would be greatly appreciated.
Thanks,
James
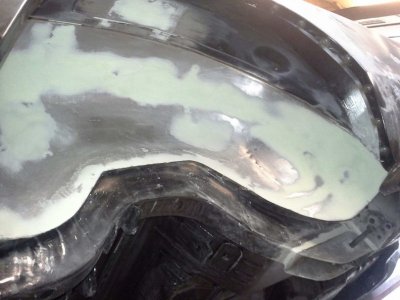