- Local time
- 7:59 AM
- Joined
- Oct 16, 2014
- Messages
- 29,596
- Reaction score
- 73,187
- Location
- Salisbury, Vermont
Hi guys, I have a problem on the header panel i'm fabbing up for the "Express". I cut the first 8 inches from my '67 Coronet hood for the header and I don't want the contour lines that flow in from the front outside corners so I hammer and dollied them flat. Bone head move. That stretched the metal and put a bow in the sheets edge. I need to unstretch those two areas while still keeping the flat surfaces I created.
Help please? Any creative suggestions appreciated. Thanks!
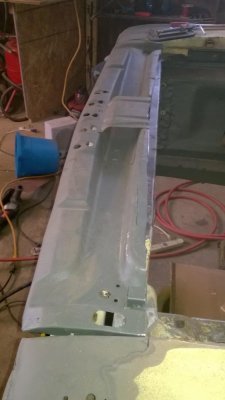
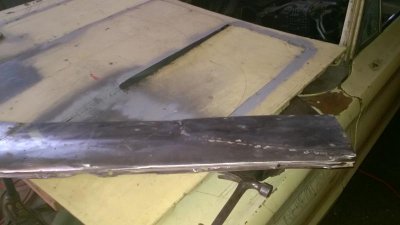
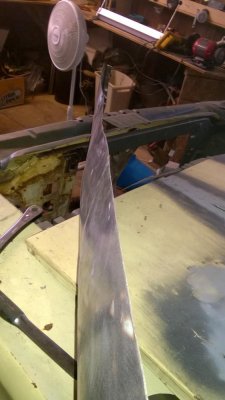
Help please? Any creative suggestions appreciated. Thanks!
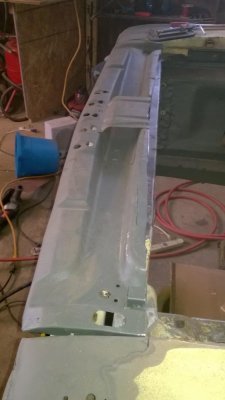
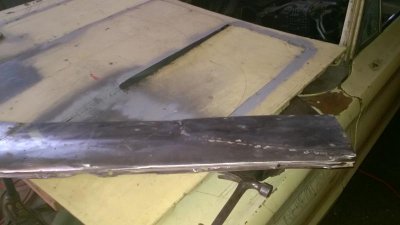
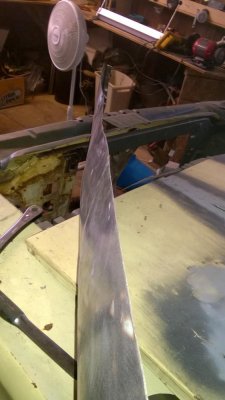