chgr1
Well-Known Member
- Local time
- 7:00 PM
- Joined
- Feb 5, 2013
- Messages
- 77
- Reaction score
- 173
- Location
- Cedar Creek Near Austin Texas
Now we temporality attached the new gutter and the new quarter to get them aligned to each other, keep in mind that these two new pieces also have to align with the deck lid. We temp re-installed the deck lid to check the overall alignment, there will be some additional body work that will have to be done but the overall alignment looks to be ok. Even modifying the new trunk gutter slightly to get it to fit under and next to the new quarter.
You have to keep in mind that the new gutter and new quarter will not fit exactly like the originals. The gutter especially is not made exactly like the original, but it is the best that is available. The bends are more rounded than the original. You have to get it lined up the best you can and then do some cosmetic body work. We still have to deal with replacing some of the forward rounded corner next to the deck lid hinge.
Once we got things fitted the best we could, we then started to attach the gutter to the trunk body and then to the new quarter. Also started to attach the rest of the new quarter. Down under the rocker panel was especially difficult to get the new quarter clamped to the body.
We spent a lot of time fitting these pieces together the best we could. We now have everything attached where it is going to go. All the securing screws are in all around the new quarter. next we will start to remove the screws one at a time and weld everything together.
We now have over 77 hours invested in this project. We have worked on some things that I haven't reported on yet, like work on the front fenders. We still have a lot to go.
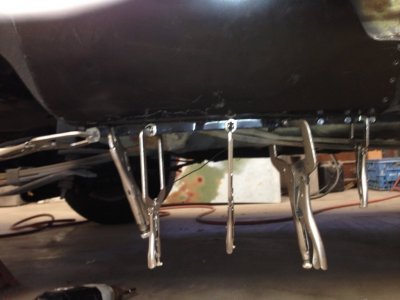
You have to keep in mind that the new gutter and new quarter will not fit exactly like the originals. The gutter especially is not made exactly like the original, but it is the best that is available. The bends are more rounded than the original. You have to get it lined up the best you can and then do some cosmetic body work. We still have to deal with replacing some of the forward rounded corner next to the deck lid hinge.
Once we got things fitted the best we could, we then started to attach the gutter to the trunk body and then to the new quarter. Also started to attach the rest of the new quarter. Down under the rocker panel was especially difficult to get the new quarter clamped to the body.
We spent a lot of time fitting these pieces together the best we could. We now have everything attached where it is going to go. All the securing screws are in all around the new quarter. next we will start to remove the screws one at a time and weld everything together.
We now have over 77 hours invested in this project. We have worked on some things that I haven't reported on yet, like work on the front fenders. We still have a lot to go.
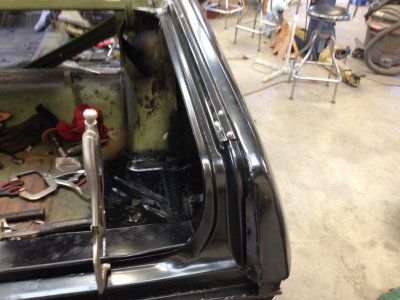
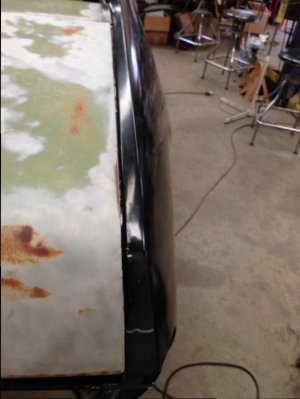
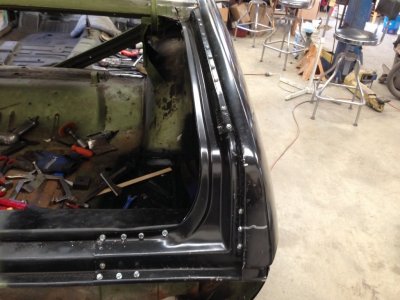
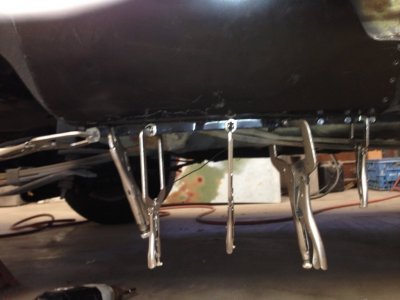
Last edited: