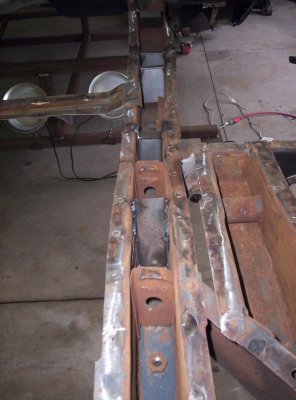
- - - Updated - - -
So after a hard week I got about 90% of what I wanted done! So I'll kinda breeze through here a little. First I found on my car it was easier to hang the 1/4s in place and work backwards to we tubs, trunk floor trunk ext.'s, tail light panel. It was just easier to get everything to mate up. So I mocked everything up, checked my gaps, body lines, window opening, and for level then put sheetmetal screws in for referance to reassemble. Once apart again I put my frame rail gussets in (see above) then POR 15 them.
- - - Updated - - -
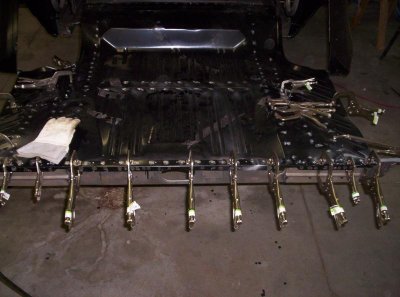
- - - Updated - - -
Screwed the trunk floor back on and started plugging the 188 holes I just drilled in it, then sanded smooth with a flapper wheel on the grinder. Note here, I bought 2 of the cheap harbor frieght grinders on sale for 10$ a piece and have a cut off wheel and a flapper wheel on them, plus my good one with the grining wheel so I'm not constantly changing out the wheels! Speaking of Harbor frieght also bought 20 vise grips on sale for 3.99, SCORE!!!!
Next I moved to the outer wheel tubs and did the same with them.
- - - Updated - - -
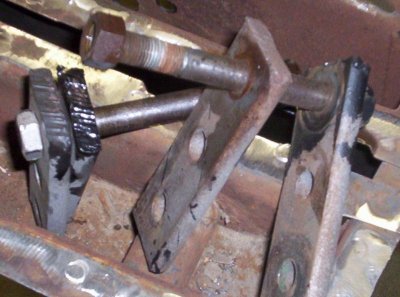
BTW check out these custom tourched shackle I took off!
- - - Updated - - -
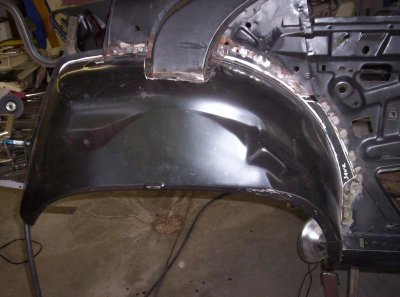
- - - Updated - - -
Next I hung the 1/4 back on and rear window filler. Once in place and real close I screwed them down and started welding at the door jam, then down across the rocker, back to roof seam, then to tail light panel. Then back to outer wheel wells.
- - - Updated - - -
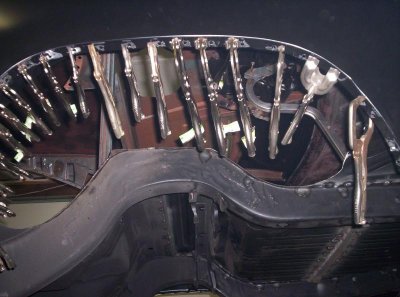
- - - Updated - - -
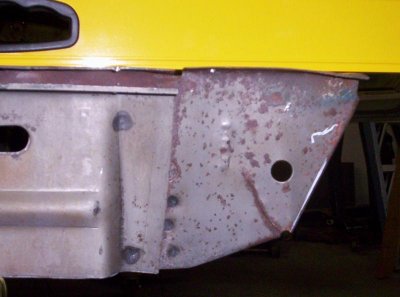
- - - Updated - - -
You can see how far off the trunk ext. pads were off from right to left from the factory! so I corrected that a little.
- - - Updated - - -
- - - Updated - - -
I can't stress enough that get your body lines right & gaps right also. I know it's a pain I had the 1/4's on and off at least 4-6 times per side getting everything as close as I could. I have 1/4 gaps at the doors and trunk and the trunk was a stinker getting right. Another thing check your drip rail piece that goes in the rear 1/4 window also I was lucky to catch that one.
- - - Updated - - -
- - - Updated - - -
- - - Updated - - -
So theres the left mini tub mocked in place. Looks pretty good huh. I rolled a step in the 2 pieces so when I weld it and sand it smooth it should look pretty clean. I'll have the body guy give it a swipe of filler if needed. Oh I forgot I used Eastwoods rocker panel sealer for the inside. stuff works great. I did combine to of the 18" hoses so I could make sure I got overlap at the middle of the rocker when coming from both ends. Also used it on frame & to shoot in between the trunk panesl to seal it up a little. 6 cans in all.
- - - Updated - - -
I finally feel like I'm over the sheet metal hump

If anyone has questions feel free I kinda condensed this a lot.
- - - Updated - - -
Also still on track to drop her off at the body shop 1st of Aug. :0}