- Local time
- 5:00 PM
- Joined
- Apr 13, 2012
- Messages
- 35,575
- Reaction score
- 125,330
- Location
- Granite Bay CA
A new trend that is gaining momentum is the habit of making our classics handle better than they did when they were new. Most members probably already know about the benefits of poly bushings, better shocks, wider tires and larger Sway bars. I wonder how many have ever considered how their K member affects the way that their cars handle?
On another forum, I started a thread about how welding critical areas on the k member can improve your steering precision and feel. This really isn't anything new. Firm Feel Inc has been doing this for years and still offers this service. Mopar Action magazine has had articles where they mention it as well.
As stock, the k member worked as intended. Skinny tires, conservative alignment and a 5 year lifespan.... Yeah, mission accomplished. Now we have these cars that Ma Mopar probably never thought we'd STILL be driving, 40 years later with tires twice as wide. Something has to give, right? The steering box mounts on our cars are an area that can REALLY benefit from reinforcement. If you are curious, Have someone turn the steering wheel as you look at the steering box. See how it flexes? Imagine how much worse it gets as you hit a bump in a turn! It flexes 3/8" each way while sitting still!!??
Looking at a bare K member, you can see the unsupported areas that allow that flex to occur:
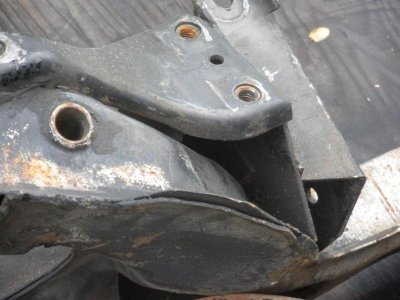
On another forum, I started a thread about how welding critical areas on the k member can improve your steering precision and feel. This really isn't anything new. Firm Feel Inc has been doing this for years and still offers this service. Mopar Action magazine has had articles where they mention it as well.
As stock, the k member worked as intended. Skinny tires, conservative alignment and a 5 year lifespan.... Yeah, mission accomplished. Now we have these cars that Ma Mopar probably never thought we'd STILL be driving, 40 years later with tires twice as wide. Something has to give, right? The steering box mounts on our cars are an area that can REALLY benefit from reinforcement. If you are curious, Have someone turn the steering wheel as you look at the steering box. See how it flexes? Imagine how much worse it gets as you hit a bump in a turn! It flexes 3/8" each way while sitting still!!??
Looking at a bare K member, you can see the unsupported areas that allow that flex to occur:
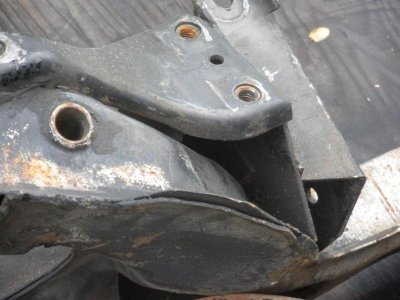