Malex. Thank you very much for the response. Gives me a direction to head. The LH upper and lower replacement panel have been ordered. Hopefully they will be here before next weekend....and they won't require much modifying....lol
I was kinda of hoping there would be some additional input, ie: from the people that frequent this site, that have been there and done that.
Just looking for other ideas/ solutions on the cowl area.
But you know what, it doesn't matter, we will keep, keeping on.
I worked on the 64 today. I began cleaning up all of the rust issues in the lower cowl area...prognosis not good. This area will require additional work. Unfortunately no one makes replacement panels for this area.
If anyone has a short cut, other then fiber glassing, I am all ears. The area could be sand blasted, but, it wouldn't matter what method of rust removal a person used, it will still end up needing replacement metal.
For the picture hounds, here is a look at what I am referring to:
Its total Swiss Cheese. I plan on replacing the metal in sections around the wiper arm. Thus not cutting out a large area at any time. Hopefully minimizing warping...
Below, The plan is to remove the panel at the seam (drill out tack welds), rebuild/ repair both the inner and outer panels, along with the fresh fresh air box. replacing the rotten metal on the bench and reinstalling.
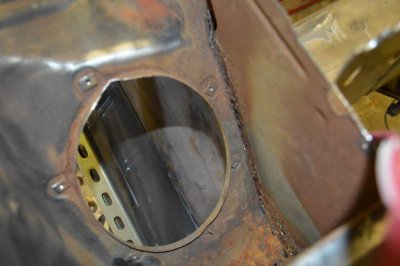
Old cars, don't ya just love them? The more you dig in, the deeper you get........it must be a sickness...
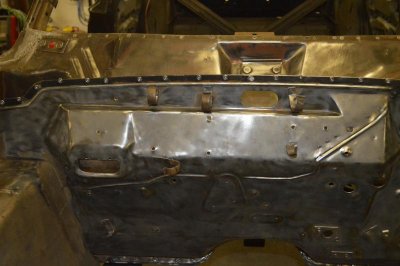