carnalsupply
Well-Known Member
Today I reached a milestone; the firewall set-back is permanantly in place so now I can move on to pedal, seat, and steering column placement, as well as finishing the floor and tunnel, all of which had to be held off until I finished the set-back.
I have to admit, I have really had doubts over the years, wondering if I would ever actually get to this point, but now that I have I feel totally energized about pushing forward and can't wait to get to the shop every day.
Here are some shots of the completed firewall, though final welding will wait for the car to be mounted on the rotisserie so I can get easy access and not have to weld upside down, etc.
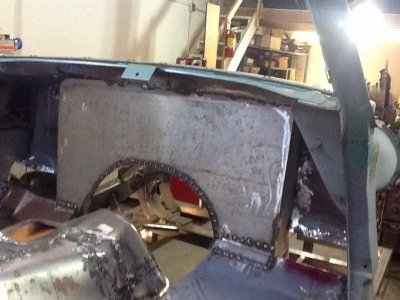
I have to admit, I have really had doubts over the years, wondering if I would ever actually get to this point, but now that I have I feel totally energized about pushing forward and can't wait to get to the shop every day.
Here are some shots of the completed firewall, though final welding will wait for the car to be mounted on the rotisserie so I can get easy access and not have to weld upside down, etc.
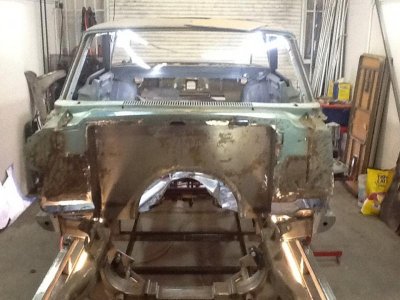
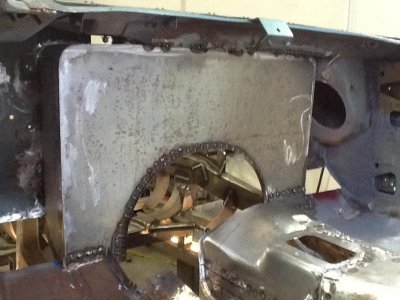
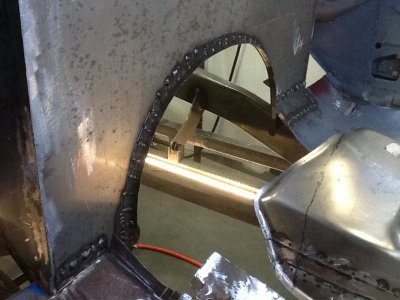
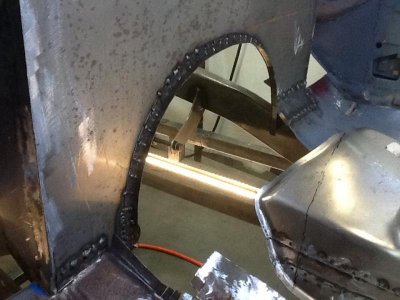
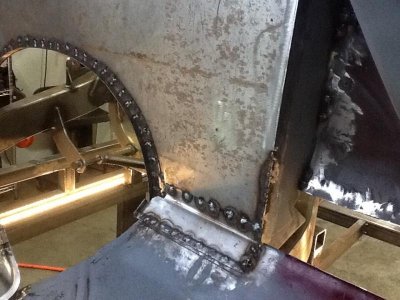
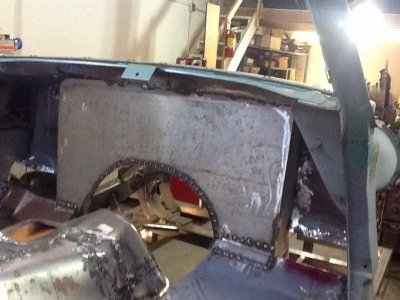