My friend has a Bridgeport and it's DRO - and programmable ( sorta a CNC - 2 axis - with a manual 3rd axis - machine ).
He's teaching me how to use it and it's amazing !
Our plan is for me to build a bigger shop, and merge both of our shops together into one shop - he's amazing on the work that he does
( and I'm blessed to be able to learn from him )
And I'm also looking forward to the learning . . .
With the lathe, I found the funniest thing was that I was using the lathe to make adjustments to the parts for attaching the chuck so that I could get it adjusted - which finally resulted in me getting the total run out on the chuck to 6/10 . . . ( I so wanted to push it further and get it less - but that is really incredible as it sits )
Your lathe, when set up, is much more than a cutting tool. It is a measuring device. And feel free to think outside the box with it.
Example--I made a fireplace screen by winding stainless and copper wire on my lathe using the table threading feed.
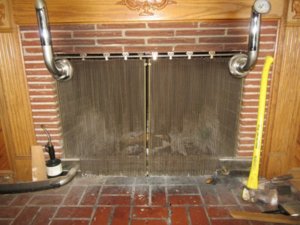
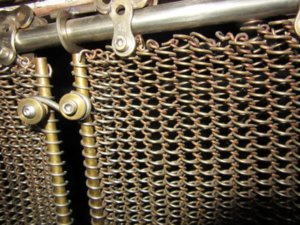
Last edited: