Durability depends mostly on prep and clean metal, with application and curing standards taking a close second.
When it started decades ago, powder coating was reserved for military applications. (I never served so someone who has is invited to chime in on how it held up in Afghanistan or Iraq under very harsh conditions.)
Then the process filtered down to manufacturers (washers, dryers, etc.) who went 'assembly line' with conveyor belt systems. My own washing machine peeling in sheets around the bleach dispenser -- revealing shiny metal or rust -- shows me their prepwork is crap and they don't care beyond getting my money for the product.
The Green Push the last 30 years has seen powder coating replace paint lines in nearly every industry requiring a finish on metal, plastics and even wood. Advancements are common.
Classes are available but focus more on basics OR profitability. Most YouTube how-to videos are done by the blind leading the blind, often more harmful than helpful.
Now in my 24th year after 8 as a hobbyist restoring my Barracuda, I know everyone has to start somewhere. The problem these days are the ones who coat a couple brackets and open a shop rather than bothering to learn the craft.
There are no formal "industry standards," no regulation or accountability as other professions require, so Mr. Car Guy is left to suffer the consequences when his rear end housing comes home full of media or the Delrin liners separating his leaf springs melt, are not replaced, and he puts them back on his car.
Sorry this turned into a novel. There are just far too many factors and rookies involved to make a blanket statement that powder coating is a good or bad idea for anything that actually gets used. It's all in the prep.
The military uses a coating refered to
as CARC. Similar in application to
powdercoating. I worked in the military
vehicle design industry for many years,
and never witnessed the smooth,
shiny, near perfect finishes that
powdercoating offers to the public
for their everyday hotrod. While
powdercoating does offer a tough
resilient coating, there are limitations
as to where this application will last
longer than ordinary every day paint.
If a powder coat surface becomes
damaged via a scuff or scratch, there
is no known repair other than
a complete stripping, and
re-powdercoating of the entire part.
This can get rather pricey when
dealing with entire vehicle frames.
I damaged the powdercoat finish
while installing the bed on my frame.
I'm lucky where the gouge did not
prenetrate to bare metal and
the remelting of the powdercoat
with a bic lighter took the rough
edges off and smoothed out the
blemish.
As with any finished surface, once
the potential for rust and or
corrosion enters the picture....it's
toast.
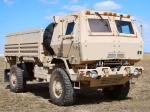
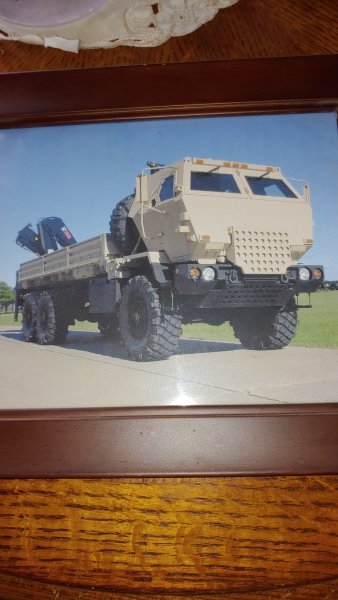
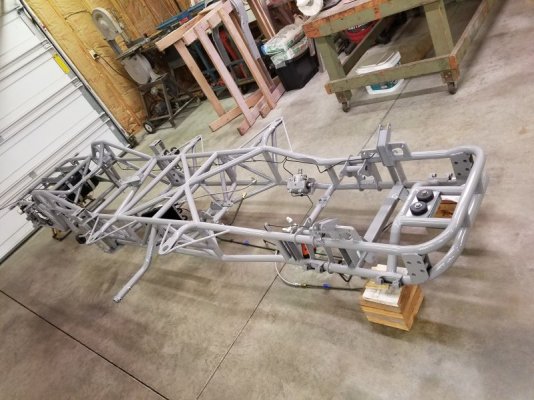