dpstark2
Well-Known Member
I got tired of my worn out 25 gallon Crafstman compressor (30 years old) not keeping up with with tools, so I invested in this 60 gallon Quincy unit. A friend has the 80 gallon unit, and it's fantastic, but I couldn't justify the 50% price premium for 33% more capacity and < 2cfm more. I plumbed four drops in the garage using the RapidAir Maxline system. It is easy to use, but what a PITA to straighten the tube... that's a two man job, minimum. The compressor outlet has a coarse filter, regulator, and fine filter attached. In the future, I'll be adding a desiccant system.
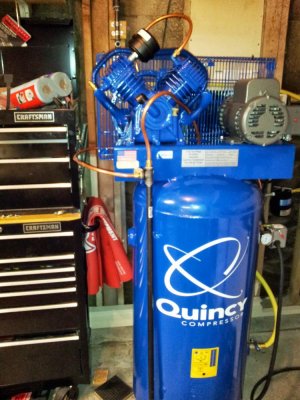
However, the desiccant's job is greatly reduced by the addition of an aftercooler. It's a B&M trans cooler with a 230V, 1100 cfm fan wired off the compressor motor. This thing is flat amazing (bonus points go to my friend that got this thing rolling for that idea). The cooler drops air temps 200F from the pump to the tank. The tank, previously hot to the touch after filling, remains nice and cool. And the drip leg on the the cooler gets (I estimate) 75% of the water out before the tank! Each drop in the garage has it's own drip leg, and they have yet to produce a single drop of moisture. That fan, by the way, needs a guard. It can remove fingers.
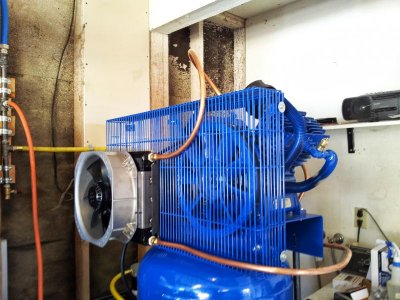
This was not a cheap project. But the 50k hour pump should last basically forever it sure makes life easier. Would you believe it's even quieter than my old Craftsman? It is.
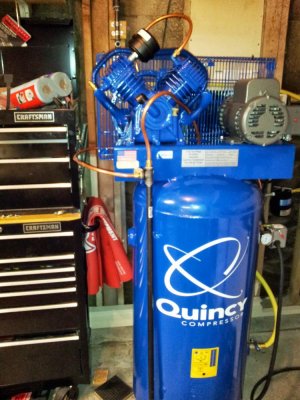
However, the desiccant's job is greatly reduced by the addition of an aftercooler. It's a B&M trans cooler with a 230V, 1100 cfm fan wired off the compressor motor. This thing is flat amazing (bonus points go to my friend that got this thing rolling for that idea). The cooler drops air temps 200F from the pump to the tank. The tank, previously hot to the touch after filling, remains nice and cool. And the drip leg on the the cooler gets (I estimate) 75% of the water out before the tank! Each drop in the garage has it's own drip leg, and they have yet to produce a single drop of moisture. That fan, by the way, needs a guard. It can remove fingers.
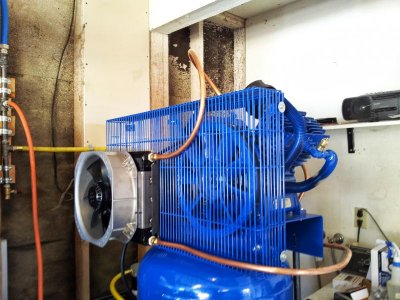
This was not a cheap project. But the 50k hour pump should last basically forever it sure makes life easier. Would you believe it's even quieter than my old Craftsman? It is.