mopar4don
Well-Known Member
Now it was time for the rockers where I started on the passenger side.

Spot welds galore! Thanks to this site I knew there were some spot welds on the inner wheel house so I removed those.
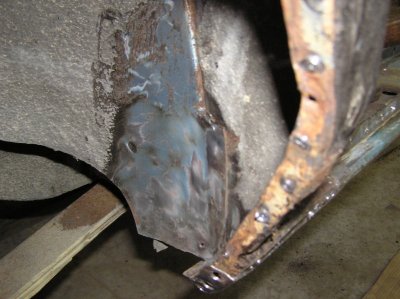
Then I moved to the front A-pillar or where the front of the jam meets the rocker.
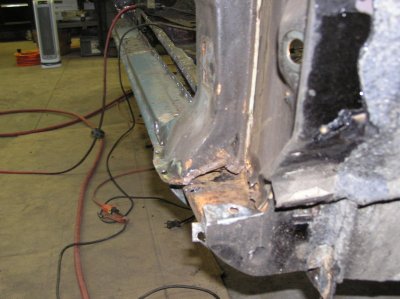
The biggest problem I had, was not realizing there was a spot weld or maybe it was a factory weld, inside the A-pillar.
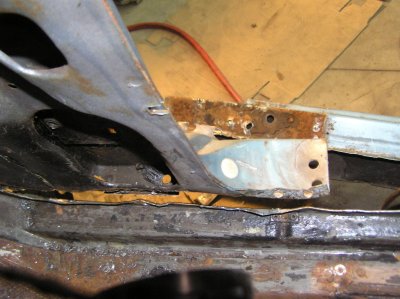
I didn't know this until I had pried the rocker down far enough to see underneath it.
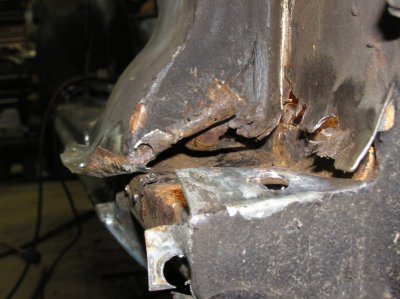
It took a while, (a day and half) but I finally got it!
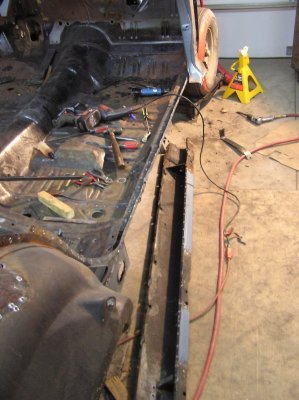
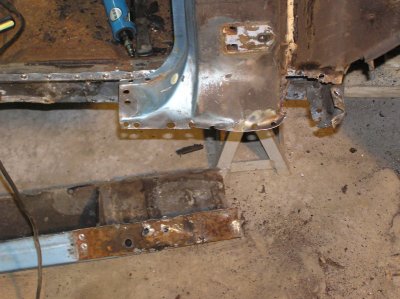
Next I removed the foot well floor pan.
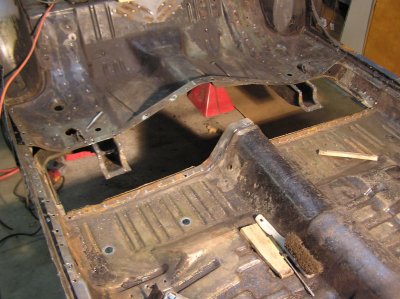
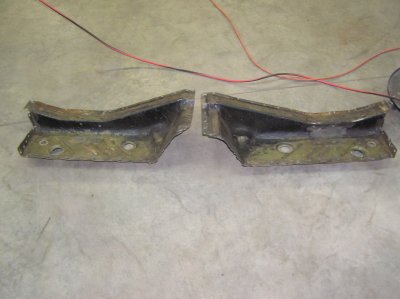

Spot welds galore! Thanks to this site I knew there were some spot welds on the inner wheel house so I removed those.
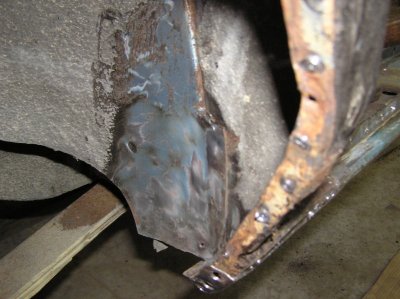
Then I moved to the front A-pillar or where the front of the jam meets the rocker.
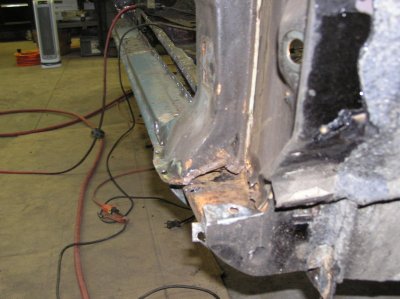
The biggest problem I had, was not realizing there was a spot weld or maybe it was a factory weld, inside the A-pillar.
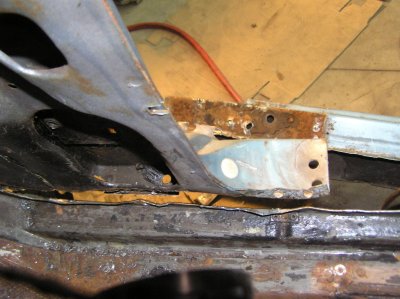
I didn't know this until I had pried the rocker down far enough to see underneath it.
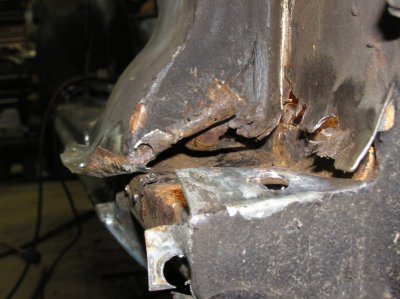
It took a while, (a day and half) but I finally got it!
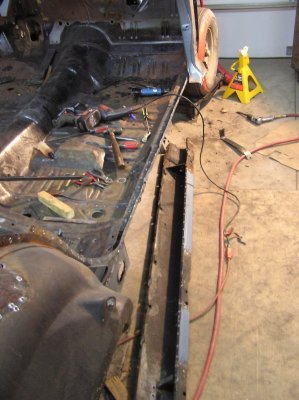
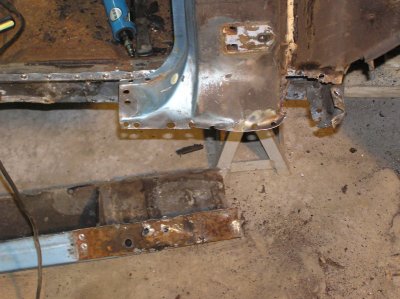
Next I removed the foot well floor pan.
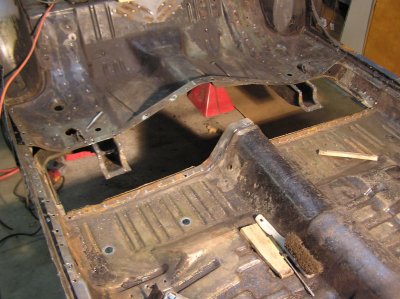
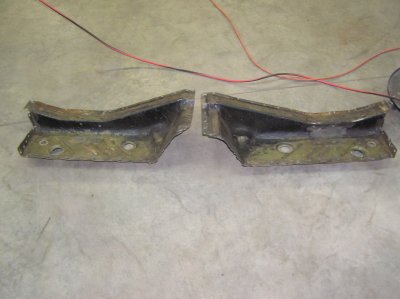